Augmented Reality in Industrial & Manufacturing
The manufacturing and industrial sectors are embracing a digital revolution where augmented reality (AR) is transforming traditional processes. AR is a powerful tool in the quest for operational excellence, from streamlining product design and assembly to revolutionizing on‐the‐job training and maintenance. With platforms such as Unity Industry leading the charge in real‑time 3D experiences, industrial companies can now integrate immersive technologies into every stage of their workflow. This article explores augmented reality's benefits, applications, and future trends in industrial and manufacturing settings, drawing on real-world examples and case studies provided by Unity.
What is Augmented Reality?
Augmented reality is a technology that overlays digital information—images, text, 3D models, and videos—onto the real world in real time. Unlike virtual reality (VR), which creates an entirely artificial environment, AR enhances users' existing view of their surroundings. In industrial contexts, AR applications might display operational data on equipment, provide step‑by‑step maintenance instructions, or enable interactive design reviews.
AR’s ability to blend the physical with the digital has made it invaluable for modern manufacturing processes. By presenting critical information directly into the user's field of view, AR reduces the need to consult separate manuals or screens, improving safety and efficiency. This seamless integration of digital data into real-world operations is at the heart of Industry 4.0, a movement emphasizing connectivity, intelligent automation, and real‑time decision-making.
The Role of AR in Industrial & Manufacturing Environments
In today’s competitive manufacturing landscape, the adoption of AR is driven by several key factors:
Enhanced Training and Skill Development
Traditional training methods often rely on paper-based manuals and classroom instruction, which may not be sufficient for complex industrial operations. AR transforms the training process by overlaying digital instructions onto the equipment itself. For example, companies like Taqtile have successfully implemented AR-based training solutions that capture expert knowledge and deliver it directly to frontline workers. This approach accelerates the learning curve and significantly reduces the likelihood of errors during critical maintenance tasks.
“With AR-based solutions, even novice workers can complete tasks with precision and confidence, replicating the step-by-step instructions originally provided by subject-matter experts.”
Improved Maintenance and Repair
AR allows users to " see through” complex machinery. By superimposing relevant data such as maintenance histories, sensor readings, and troubleshooting guides over the physical equipment, AR solutions help technicians quickly identify problems and execute repairs. This “X-ray vision” effect minimizes downtime and increases overall productivity in high-stakes manufacturing environments.
Streamlined Product Design and Prototyping
The design phase in manufacturing is no longer confined to static 2D blueprints. AR enables designers and engineers to visualize 3D models of products and production lines in real time. This interactive approach facilitates better team collaboration and allows for rapid prototyping and iterative design improvements. Simulating physical processes and predicting failures before they occur is a significant advantage in an era where time-to-market is critical.
Enhanced Collaboration and Remote Assistance
In a globalized economy, teams are often spread across different locations. AR technology allows experts to provide remote guidance to on-site workers by sharing live visual feeds and interactive annotations. This connectivity supports quicker decision-making and more efficient problem resolution. Industries such as automotive and aerospace are already reaping the benefits of such immersive collaboration tools.
Increased Safety and Risk Reduction
Safety is paramount in industrial environments. AR applications can guide workers through hazardous tasks by highlighting safety zones, displaying warning signals, and offering real-time alerts about potential dangers. By integrating AR into the safety protocols of manufacturing plants, companies can reduce accidents and protect their workforce.
Unity’s Impact on Industrial AR
Unity Technologies has emerged as a leader in real-time 3D creation, with its Unity platform at the core of many industrial AR solutions. Unity Industry provides the tools necessary to transform traditional CAD and 3D models into immersive applications that can be deployed on various devices. Unity’s extensive support for AR and VR devices makes it an ideal choice for manufacturers, whether for design visualization, training, or remote assistance.
Real-Time 3D Experiences
Unity’s technology enables the creation of interactive, real‑time 3D experiences that are crucial for modern industrial applications. These experiences allow companies to simulate their operations, test prototypes, and deliver engaging and effective training modules. For example, the Unity Industry platform supports importing, preparing, and optimizing large CAD and mesh models, ensuring that even the most complex machinery can be accurately visualized and interacted with in AR.
Cross‑Platform Integration
A key advantage of Unity is its broad compatibility across devices—from mobile phones and tablets to specialized AR headsets like Microsoft HoloLens and Magic Leap. This interoperability ensures that companies can deploy AR applications without being locked into a single hardware ecosystem. By leveraging Unity’s cross‑platform capabilities, manufacturers can create scalable and future-proof solutions.
Industry Case Studies
Several industry case studies highlight the transformative impact of Unity-powered AR solutions in manufacturing:
Taqtile’s Manifest: Revolutionizing AR-Based Training
Taqtile’s Manifest solution is an exemplary case of how AR can revolutionize industrial training. Developed on the Unity platform, Manifest captures expert instructions in real time and presents them as step‑by‑step guides to operators in the field. The system has been tested with clients such as the U.S. Air Force and the New Zealand Army, yielding impressive results. In trials, recruits using AR guidance could complete maintenance tasks with zero errors compared to multiple mistakes when using traditional methods. This reduced the skills gap and dramatically improved productivity on the shop floor.
Automotive Manufacturing and Design
In the automotive, Unity’s real-time 3D solutions expedite design reviews and prototype virtual assembly lines. Automakers leverage AR to create interactive 3D models of vehicles, enabling engineers to explore different configurations and design elements before physical prototypes are built. This reduces development time and costs while identifying and resolving potential issues early in the design process. Manufacturers have also used AR for quality control, overlaying 3D digital twins onto real-world vehicles to identify discrepancies and improve precision.
Enhancing Industrial Collaboration
Manufacturing teams are often spread across multiple locations, making efficient collaboration a significant challenge. Unity-powered AR solutions allow remote experts to virtually “step into” the factory floor, observe operations, and provide guidance in real time. This has proven especially valuable during system upgrades or when troubleshooting complex machinery. Collaborating in a shared augmented space enhances understanding, speeds up decision-making, and improves operational efficiency.
The Business Benefits of AR in Industrial & Manufacturing
Adopting AR in industrial environments is not merely about keeping up with technological trends—it brings measurable business benefits that directly impact the bottom line. Here are some of the primary advantages:
Increased Productivity
AR applications directly boost productivity by reducing the time spent searching for information or troubleshooting equipment issues. Workers can access detailed instructions and real-time data without interrupting their workflow. This leads to faster task completion and fewer errors, resulting in cost savings and higher overall efficiency.
Improved Quality and Reduced Errors
AR solutions facilitate higher precision in tasks such as assembly and maintenance. The visual overlays ensure that workers follow the correct procedures, reducing the margin for error. This improvement in quality control can lead to fewer product defects and recalls, thereby protecting the company’s reputation and reducing warranty costs.
Enhanced Worker Safety
Safety is a critical concern in manufacturing. AR applications help mitigate risks by providing live alerts and overlaying hazard warnings directly into the worker’s field of view. By ensuring that safety protocols are always adhered to, AR helps prevent accidents and minimizes the likelihood of injuries on the factory floor.
Cost Savings and ROI
The integration of AR into industrial processes often leads to significant cost savings. Reduced training times, fewer maintenance errors, and lower downtime contribute to a higher return on investment (ROI). In sectors where precision and reliability are paramount, these operational efficiencies quickly offset the upfront investment in AR technology.
Real-Time Data and Analytics
One of AR's most compelling benefits is its ability to integrate with IoT sensors and other data collection systems. This integration allows for real-time monitoring of equipment and processes, enabling proactive maintenance and rapid response to issues as they arise. With access to real-time analytics, decision-makers can optimize operations and predict future trends more accurately.
AR Trends Shaping the Future of Industrial Manufacturing
The evolution of AR technology continues to open new possibilities in industrial and manufacturing applications. As the technology matures, several trends are emerging that are set to redefine how industries operate:
The Industrial Metaverse
The concept of an industrial metaverse—where the physical and digital worlds merge to create a fully interactive, immersive environment—is becoming a reality. AR plays a central role in this environment by connecting real-time data with virtual simulations. The industrial metaverse promises to transform manufacturing by enabling advanced simulations, predictive maintenance, and enhanced collaboration across the value chain.
Integration with Digital Twins
Digital twins—virtual replicas of physical assets—are rapidly gaining traction in manufacturing. By integrating AR with digital twin technology, companies can visualize the real-time status of machinery, perform remote diagnostics, and simulate maintenance procedures before they are executed in the real world. This powerful combination enhances operational efficiency and significantly reduces the risk of errors.
The Rise of Industry 5.0
While Industry 4.0 focuses on connectivity and automation, Industry 5.0 emphasizes human-centric solutions and sustainable practices. AR will play an even more critical role in this new paradigm by enhancing the interaction between human workers and machines. Advanced AR solutions will empower workers to perform complex tasks more easily, ensuring that the human element remains central to industrial innovation.
Increased Adoption of Wearable AR Devices
The continuous improvement and affordability of wearable AR devices are set to accelerate the adoption of AR in industrial settings. Next‑generation headsets and smart glasses will become more lightweight, user‑friendly, and capable of supporting complex applications in harsh industrial environments. This evolution will further lower barriers to AR adoption, making immersive experiences accessible to a broader range of industries.
Data-Driven Decision Making
AR is increasingly being integrated with advanced analytics and machine learning platforms to provide actionable insights. With real-time data overlays, workers and managers can make more informed decisions, anticipate potential problems, and optimize processes dynamically. This data-driven approach is revolutionizing how manufacturing operations are monitored and managed.
Implementing AR Solutions in Your Industrial Workflow
For manufacturers interested in harnessing the power of augmented reality, several strategic steps can help ensure a successful implementation:
Assess Your Needs and Define Objectives
Before adopting AR technology, it is essential to define the objectives clearly. Are you looking to improve training, streamline maintenance, or enhance collaboration? Conducting a thorough needs assessment will help you determine which AR applications will deliver the most value to your organization.
Collaborate with Industry Experts
Partnering with experienced AR developers and industry experts is crucial. Companies like BrandXR offer end-to-end support—from importing and optimizing CAD models to deploying immersive AR applications across multiple devices. Leveraging such expertise can significantly reduce the implementation time and costs while ensuring a smooth transition to digital workflows.
Pilot Programs and Iterative Development
Start with pilot programs to test AR applications in a controlled environment. Use the feedback from these trials to refine the system, address any issues, and gradually scale up the deployment. Iterative development ensures that the final solution is robust, user-friendly, and aligned with your operational needs.
Training and Change Management
Integrating AR into your workflow requires a cultural shift. Invest in training programs that cover the technical aspects of the new system and help workers understand its benefits. Effective change management is critical to ensuring smooth adoption and long-term success.
Monitor and Evaluate Performance
Once your AR solution is implemented, continuously monitor its performance. Collect data on key performance indicators (KPIs) such as task completion times, error rates, and overall productivity improvements. Use this information to optimize the system further and demonstrate the ROI to stakeholders.
Unity Industry’s Suite of Tools for AR Adoption
Unity Industry provides a comprehensive suite of tools designed specifically for industrial applications. These tools help manufacturers transform their existing CAD and 3D data into interactive AR experiences that can be deployed across various devices. Key offerings include:
- Unity Industry Platform: Enables the import, optimization, and deployment of complex 3D models, allowing companies to create immersive, real-time 3D applications for design, training, and maintenance.
- Pixyz Plugin: A powerful solution that streamlines the process of converting large CAD files into optimized 3D models suitable for AR applications. This tool helps reduce load times and ensures high-quality visualizations across devices.
- Cross-Platform Deployment: Unity’s extensive hardware and software support means that AR solutions can be deployed on everything from mobile devices to dedicated AR headsets. This flexibility allows manufacturers to choose the best device for each use case, ensuring maximum impact and ROI.
Real-World Success: Transforming Manufacturing with AR
Manufacturers around the globe are already realizing the benefits of augmented reality. Consider the following success stories that illustrate the transformative power of AR:
Automotive Innovation with Real-Time 3D
In the automotive industry, companies use AR to revolutionize design, assembly, and quality control. Engineers can quickly identify design flaws and make real-time adjustments by overlaying digital models onto physical prototypes. This process accelerates the product development cycle and ensures that vehicles meet stringent quality standards before they hit the production line.
Enhanced On-The-Job Training in Heavy Machinery
Heavy machinery and complex equipment require specialized knowledge for safe and efficient operation. AR-based training programs have proven invaluable by capturing expert techniques and delivering them as interactive guides. Workers using AR headsets receive visual step‑by‑step instructions that greatly reduce the time required to master critical tasks, ultimately leading to fewer errors and improved safety.
Maintenance Optimization in Industrial Plants
Maintenance is one of the most challenging and resource‑intensive aspects of industrial operations. AR solutions provide maintenance crews with real‑time information and interactive overlays, enabling them to diagnose issues faster and precisely execute repairs. This has led to significant reductions in downtime and maintenance costs and improvements in overall plant efficiency.
The Future of Augmented Reality in Manufacturing
The continued advancement of AR technology promises to unlock even more innovative applications in industrial and manufacturing environments. As devices become more sophisticated and platforms like Unity Industry continue to evolve, the integration of AR will become increasingly seamless and pervasive. Some future trends to watch include:
Expansion of the Industrial Metaverse
The industrial metaverse—a convergence of physical and digital environments—is poised to become a game-changer in manufacturing. AR will be central to creating immersive, interactive digital twins of manufacturing plants, enabling real‑time monitoring, predictive maintenance, and enhanced collaboration across geographically dispersed teams. This shift will empower manufacturers to simulate entire production lines virtually before implementing changes on the factory floor.
Advanced Human-Machine Interfaces
Future AR solutions will feature more intuitive human-machine interfaces (HMIs) that leverage natural gestures, voice commands, and even eye tracking. These advancements will further simplify complex industrial tasks and make AR applications more accessible to workers of all skill levels. Enhanced HMIs will lead to safer, more efficient operations and greater worker satisfaction.
Integration with Artificial Intelligence and IoT
The convergence of AR, artificial intelligence (AI), and the Internet of Things (IoT) is set to revolutionize data-driven decision-making in manufacturing. By combining real-time sensor data with AI analytics, AR applications can deliver personalized, context-aware insights directly to operators. This will enable proactive maintenance, optimize production processes, and create a safer, more responsive manufacturing environment.
Broader Adoption Across Industries
While early adopters of AR have been concentrated in high-tech manufacturing and automotive sectors, the technology is gradually permeating other industries. From aerospace and energy to healthcare and retail, augmented reality is being recognized as a critical tool for enhancing productivity, quality, and safety. As more industries embrace AR, the ecosystem will benefit from increased innovation, reduced costs, and improved interoperability across sectors.
Conclusion
Augmented reality is not just a futuristic concept—it is here today, transforming industrial and manufacturing operations worldwide. By overlaying digital information onto the physical world, AR empowers workers with the knowledge and tools they need to perform tasks more accurately, safely, and efficiently. The benefits of AR are evident, from enhanced training and streamlined maintenance to real-time design visualization and improved collaboration.
Unity Industry’s suite of real-time 3D solutions plays a pivotal role in this digital transformation, offering manufacturers the tools required to harness the full potential of augmented reality. AR will continue to drive innovation in Industry 4.0 and beyond as technology evolves, paving the way for an industrial metaverse where digital and physical realities coexist seamlessly.
Manufacturers investing in AR today will improve operational efficiency and reduce costs, gaining a competitive edge in an increasingly digital world. As augmented reality becomes integral to industrial workflows, it will redefine the manufacturing landscape, making factories smarter, safer, and more agile.
For companies ready to embark on this journey, the time to invest in AR technology is now. By partnering with experienced technology providers like Unity Industry, manufacturers can turn their vision into immersive, real-time 3D experiences that revolutionize every aspect of their business.
Embrace the future of manufacturing with augmented reality—where digital innovation meets industrial excellence.
TALK TO A PRO
We're here to bring your brand to life!
Stay Connected with BrandXR
Create Augmented Reality for Free!
Create, Publish, and Measure 3D Augmented Reality Experiences Without Having to Code.
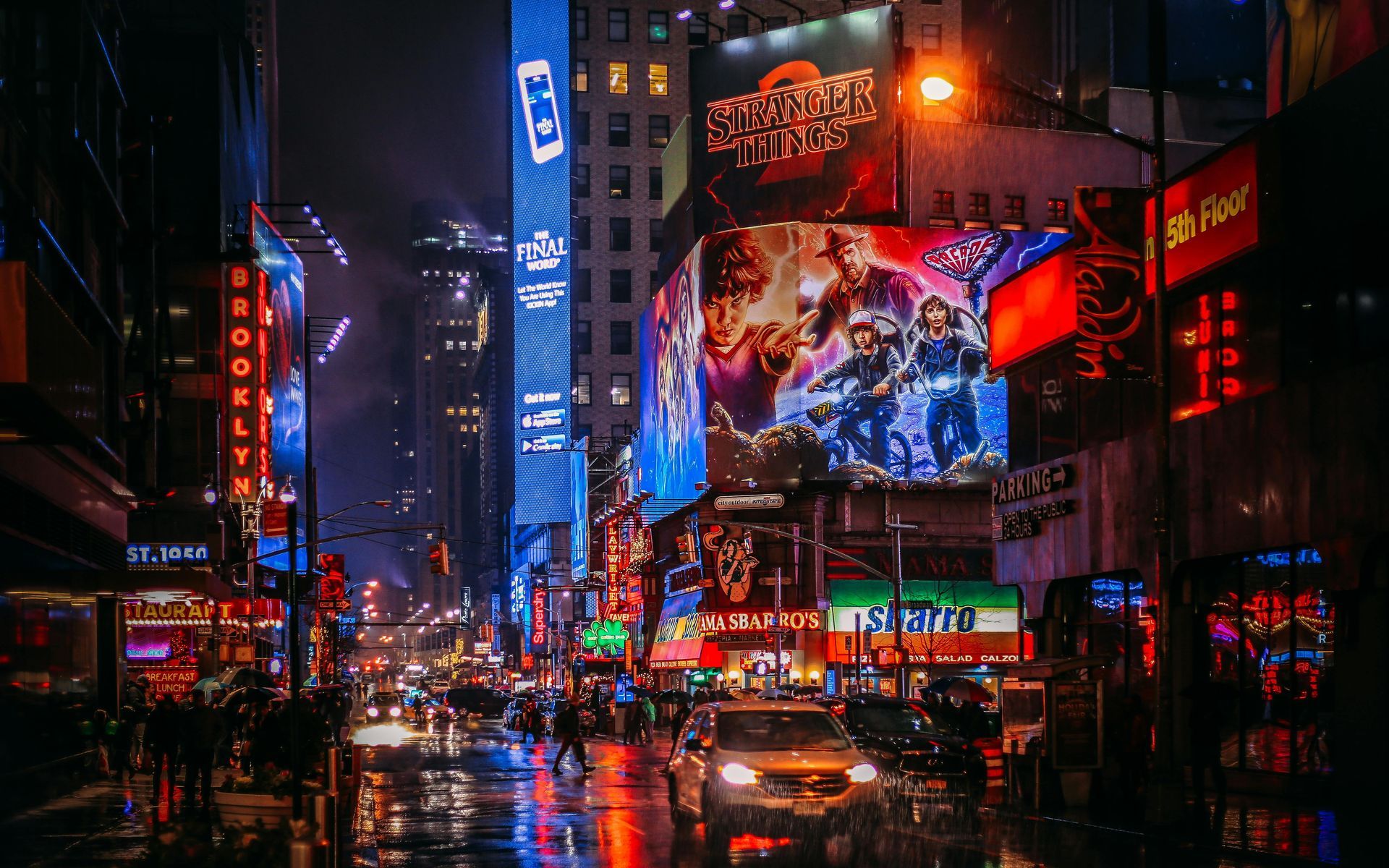
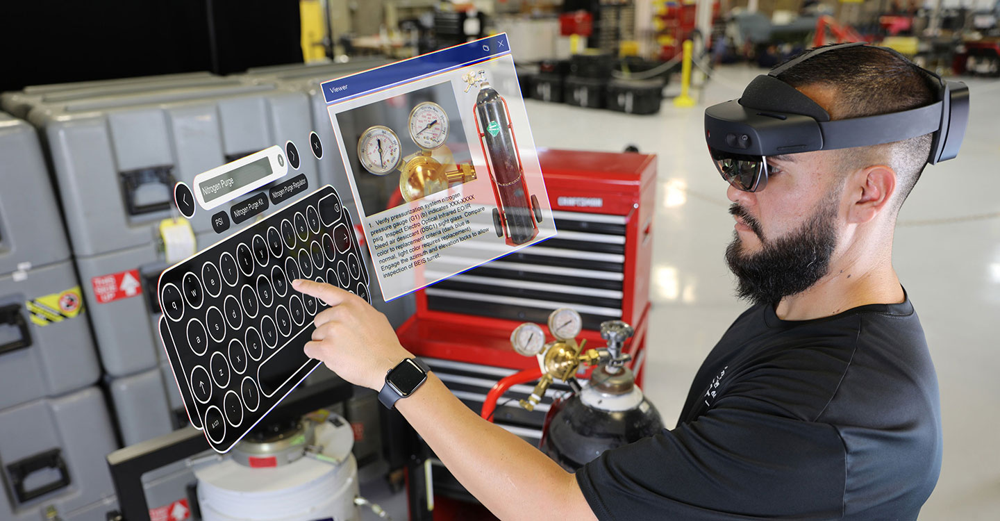
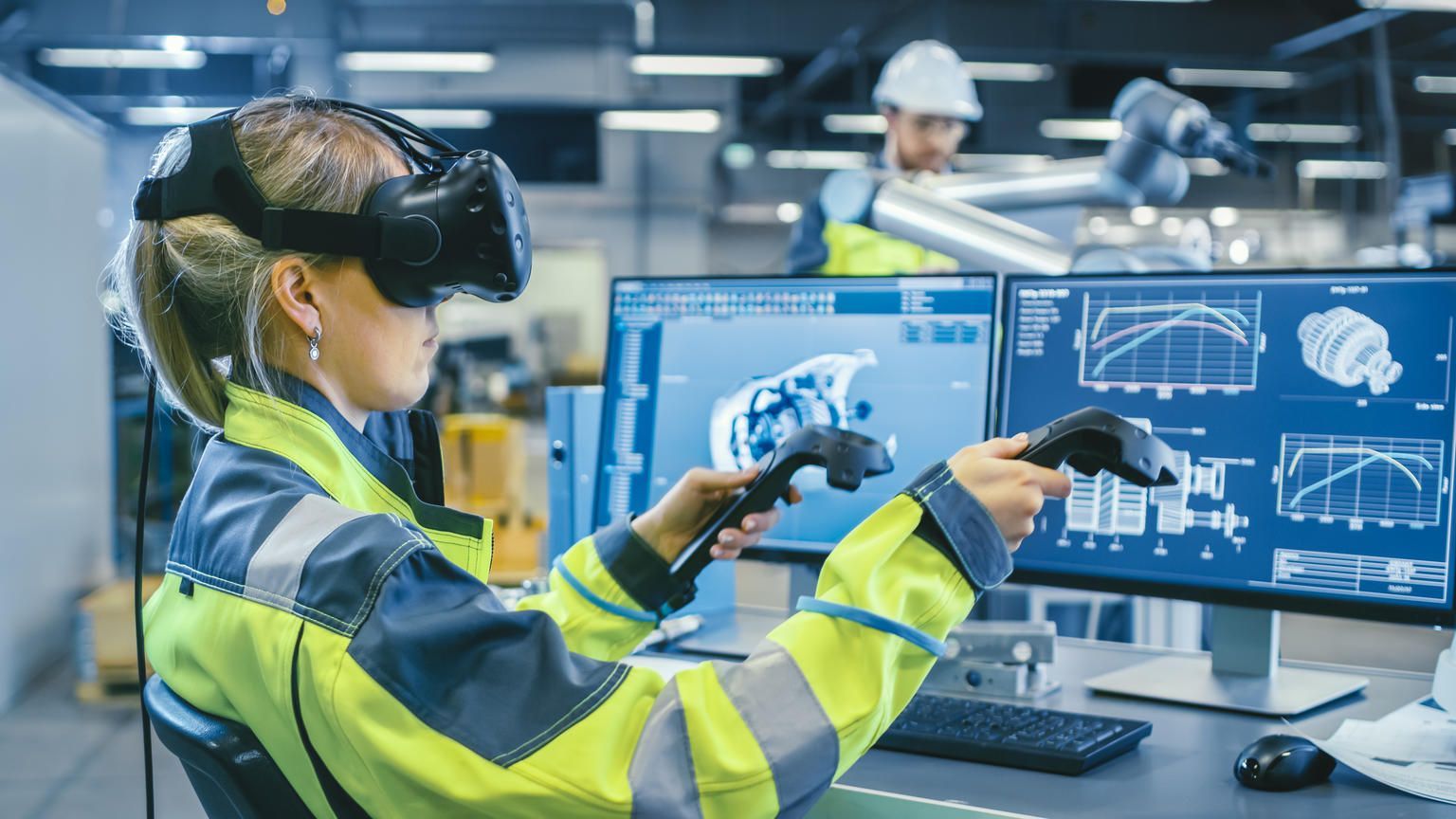
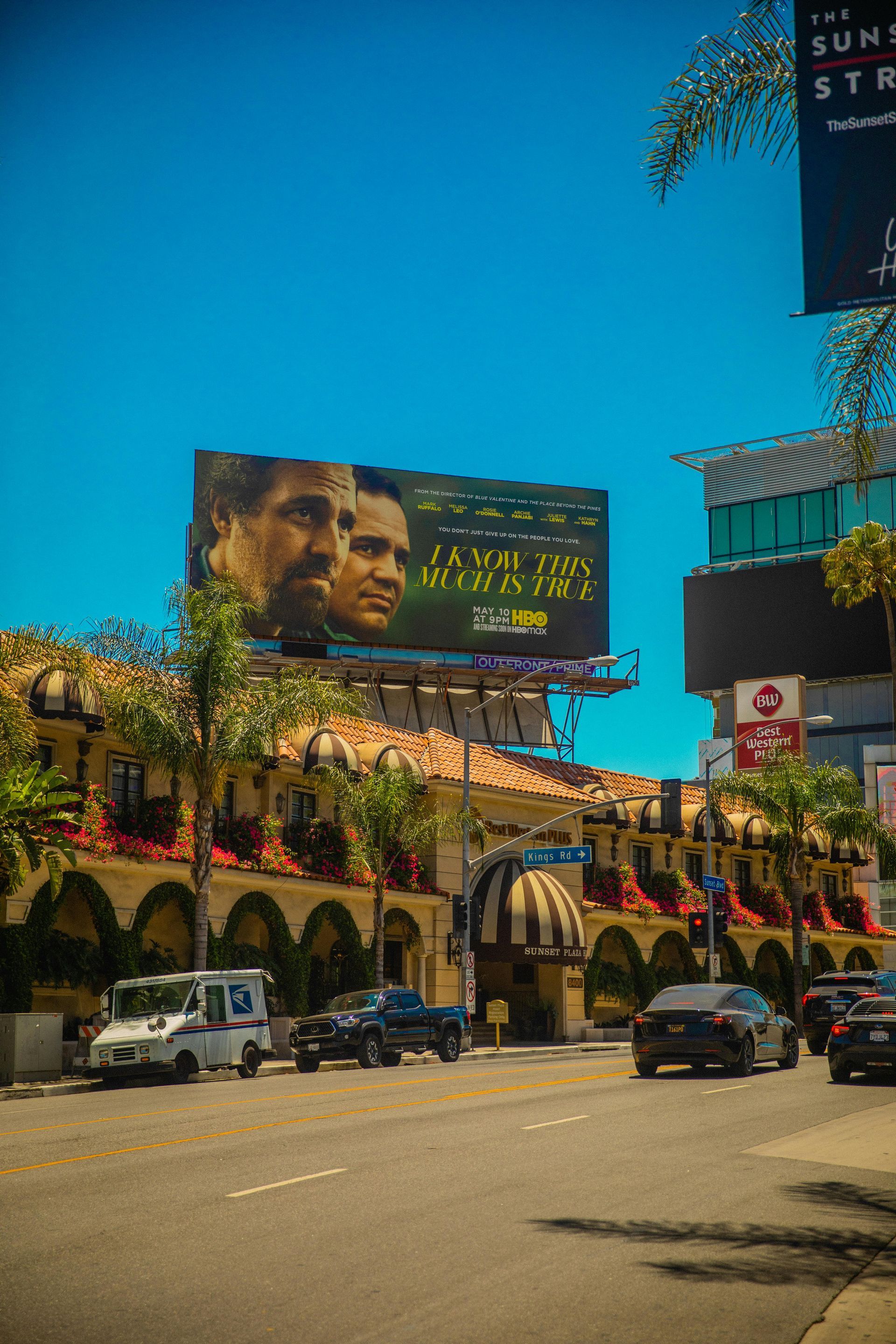
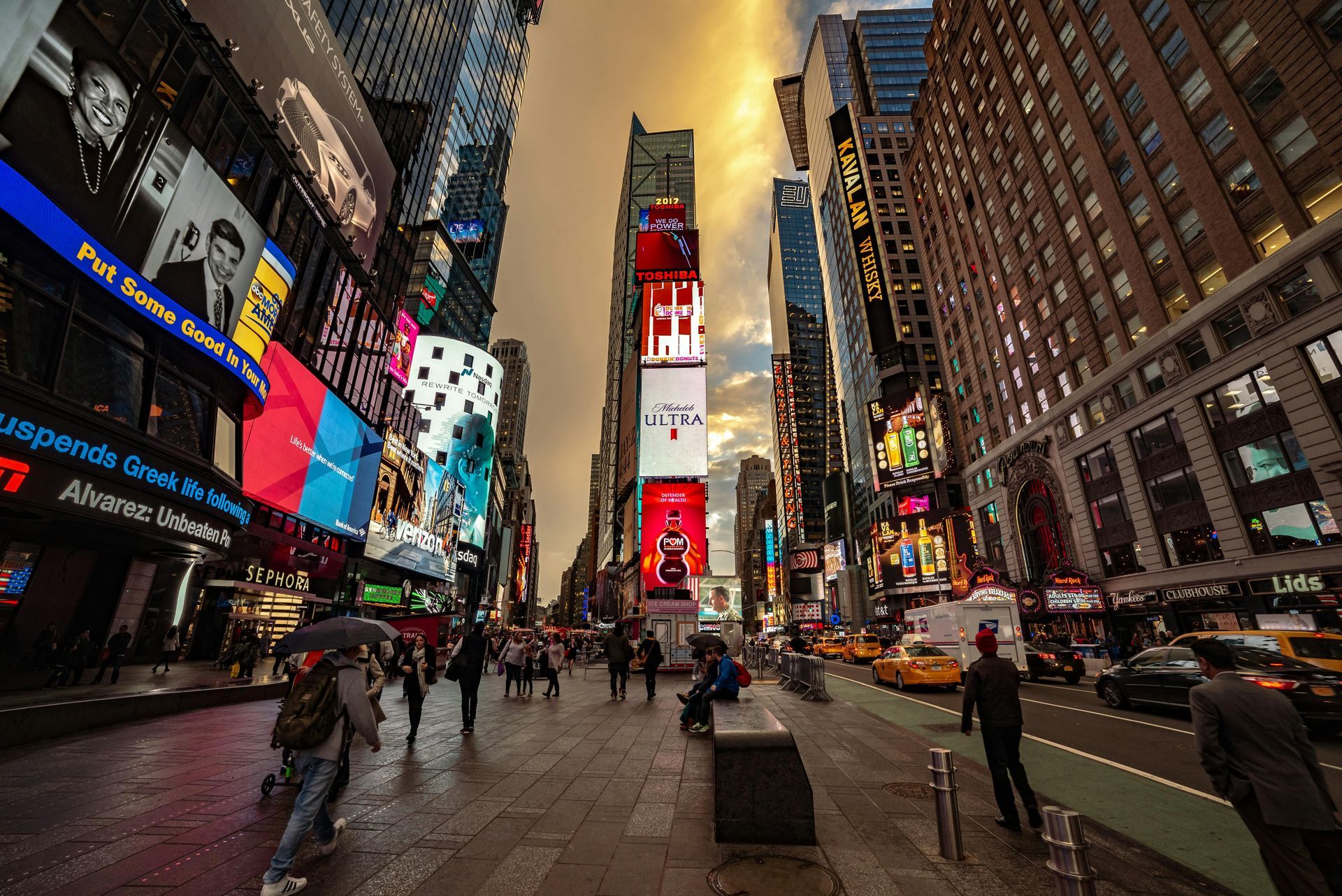
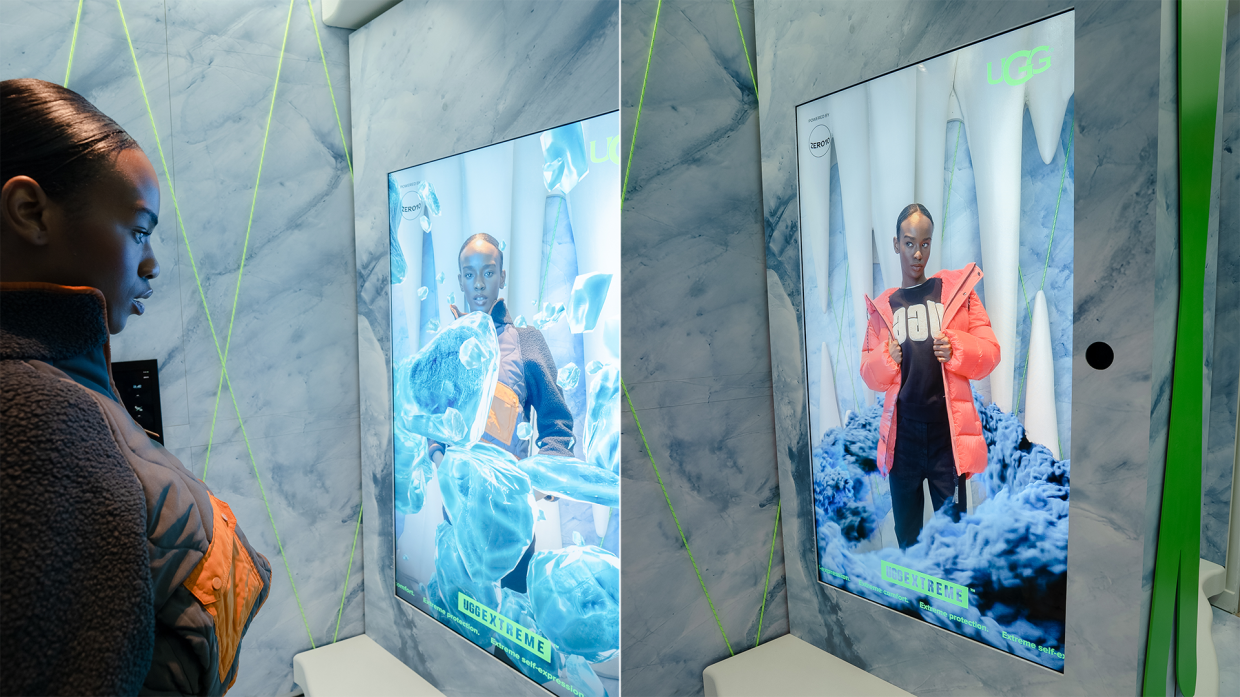
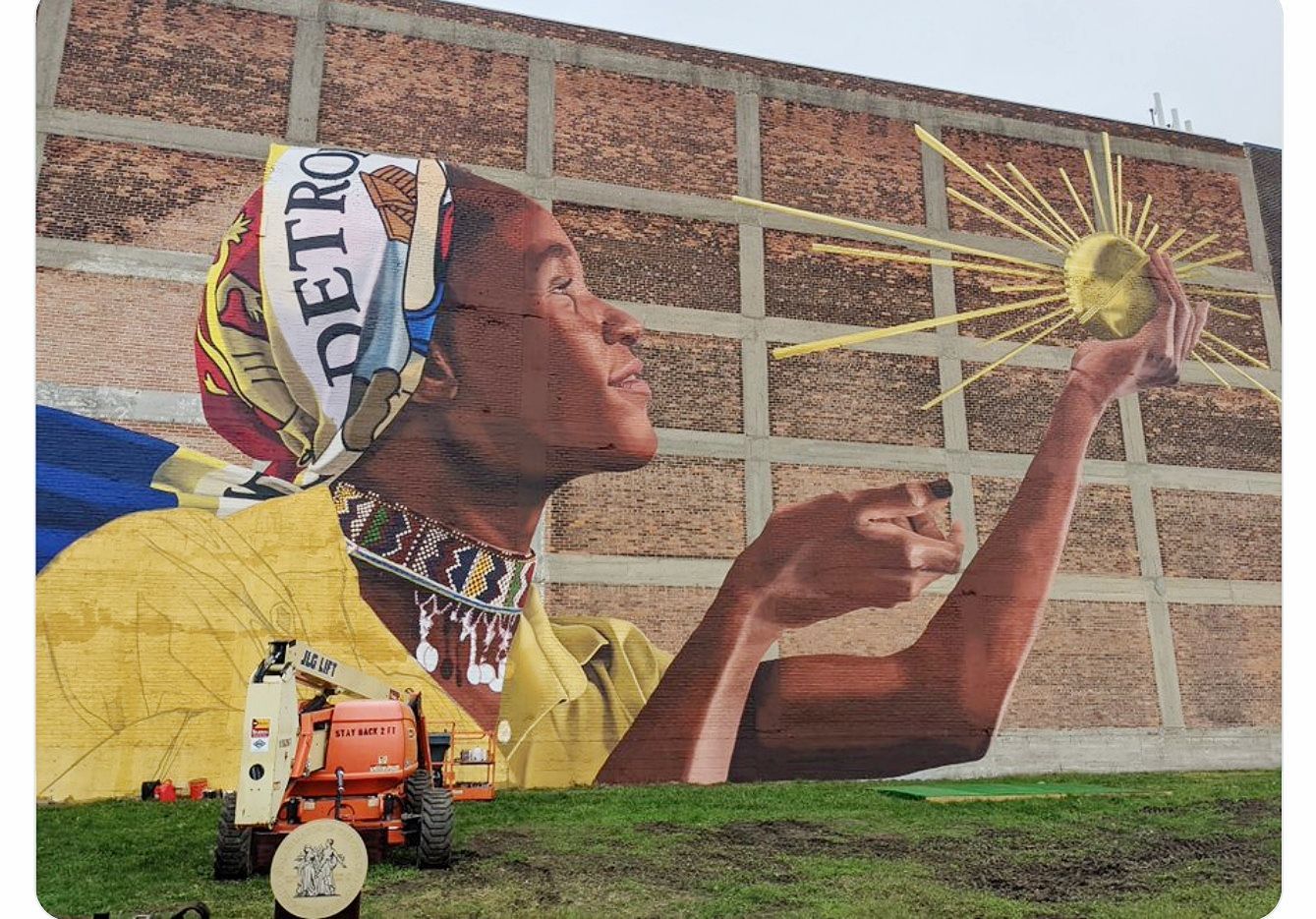
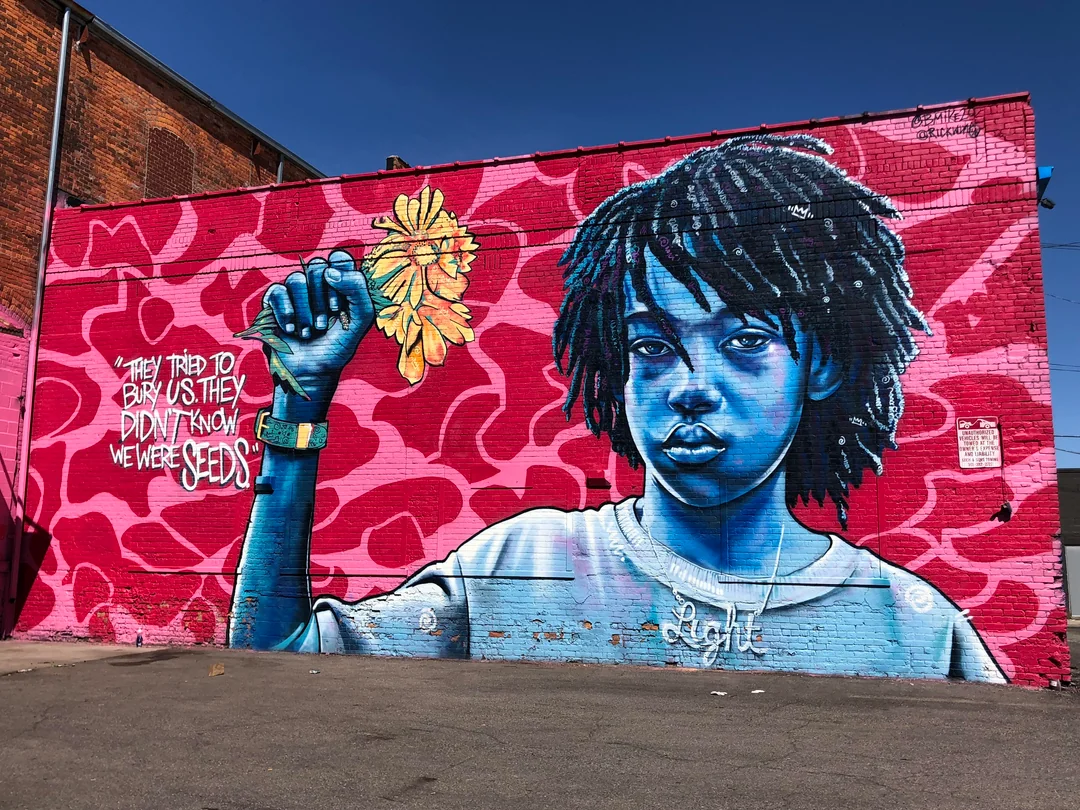
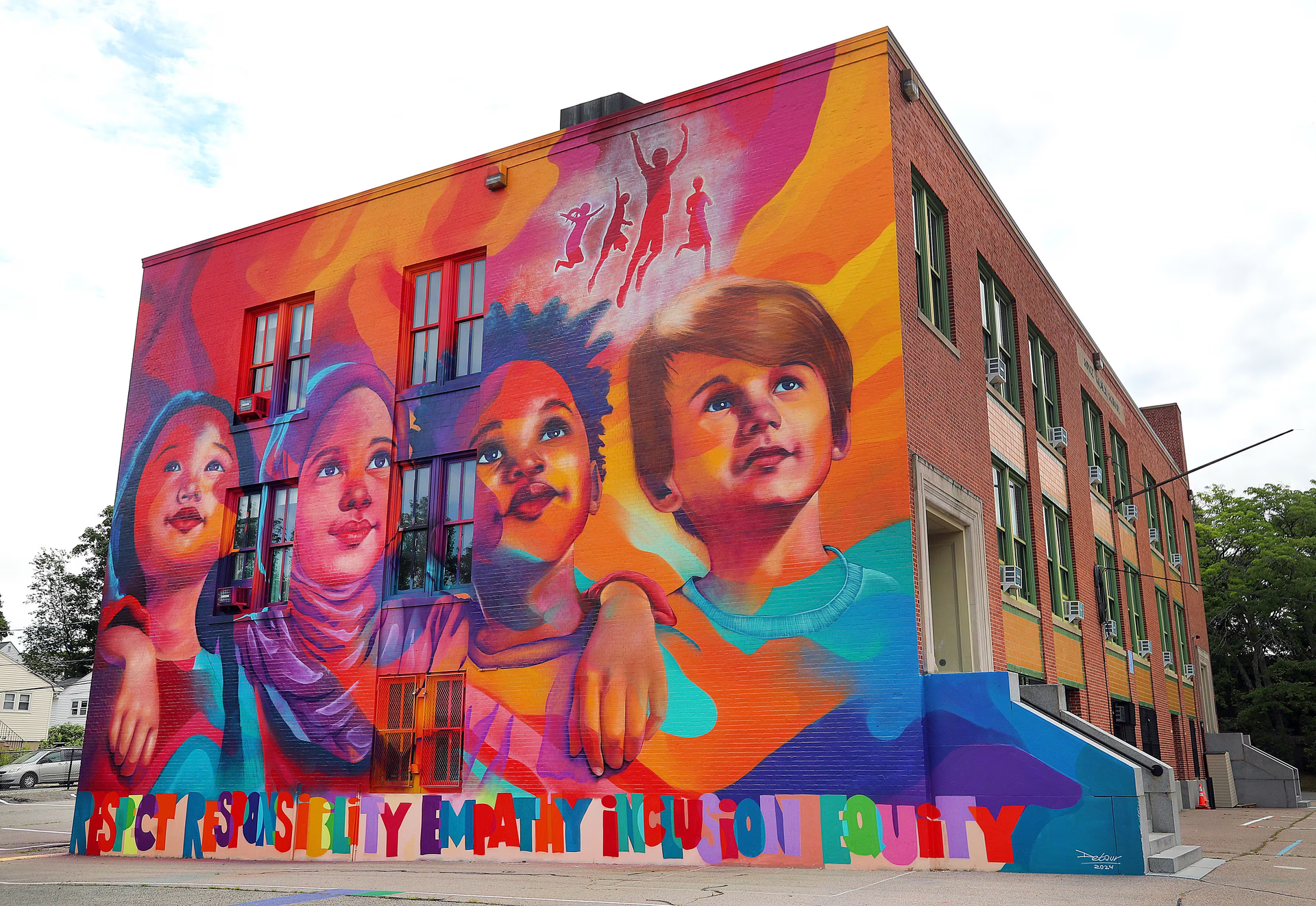